Lost-Wax Casting Process – How Does It Work?
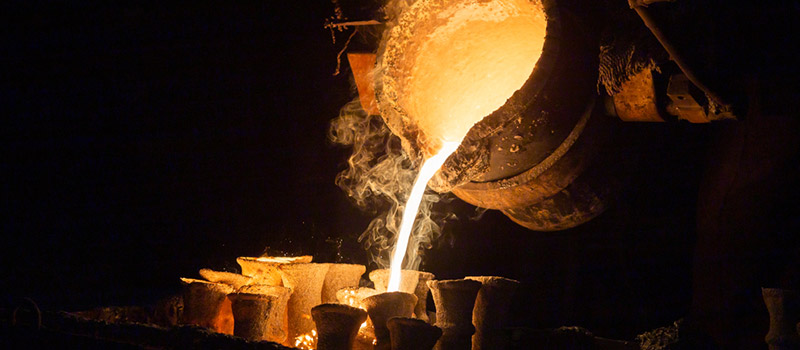
The lost-wax casting process is used worldwide, and the method is often preferred by engineers. It provides flexibility when it comes to product design and the materials used. There are applications for which you want to use the lost-wax casting process, and instances when it’s not the best casting option.
What Is Lost-Wax Casting?
Lost-wax casting (or investment casting) is a multi-step process that is used to create duplicate products from a single mold. The mold is created from the original product ensuring that all others are exact replicas. Engineers can use a variety of metals that include gold, silver, bronze, brass, and steel. The product designs range from simple to intricate.
How Long Has the Lost-Wax Technique Been Around?
The process known as lost-wax casting is not a new technique. Archeologists have found examples of the process dating back thousands of years in Mesopotamia, Africa, and South Asia. Currently, the oldest example of investment casting is an amulet attributed to the Indus Valley civilization that was carbon-dated to approximately 3,700 B.C.E or close to 6,000 years ago.
Advantages of Lost-Wax Casting
Using investment casting, instead of other product production methods comes with several advantages.
- Parts are precise and exact copies of the original.
- The casting process also ensures consistency and reduces costs for both time and labor.
- You’ll receive precision parts at a lower cost.
- Casting surface finish is far superior to that of other casting methods
- Molds are heated prior to pouring allowing for a thinner dimensions of areas such as vanes in impellers.
When to Use Lost-Wax Casting
Use the lost-wax casting process when the same part is needed for a high-volume order. If the parts need precise measurements or have a complex design, investment casting is the recommended method to use.
The lost-wax casting process is also ideal when an order calls for the same part in a range of sizes or materials. Complex designs and smooth finishes are also facilitated by the investment casting method.
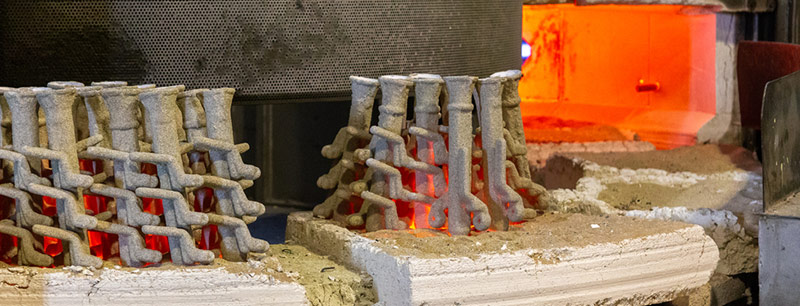
10 Lost Wax Casting Process Steps
There are several steps to creating a product using the lost-wax casting process. The steps are divided into phases to ensure every product is identical to the original mold.
1. Mold Engineering
The first step is to create the mold, also known as a wax tool. It’s either constructed from aluminum or steel and installed on a manual or automated press. If the order is smaller, a manual press is often used. To save time and labor on larger orders, engineers will install the mold on an automatic press.
2. Create Wax Models
The mold is created by filling it with liquid wax. Once the wax is cooled, the ejectors inside the mold push the form out. Now you have a model that is identical to the final product.
3. Wax Model Tree Building
After the wax model is sprayed to match the final casting, it’s glued onto a wax tree. The tree form comes with a casting funnel attached to the top that you’ll use later in the process.
4. Ceramic Slurry Coating
The next step in the process is to build a fireproof shell on the tree. You’ll submerge the wax tree into a ceramic slurry and coat it with zircon sand. Zircon sand will achieve the fine surface finish. The tree will then be submerged in a ceramic slurry and coated with silica sand. The silica sand is for strength to prevent the tree from breaking apart when pouring molten metal into it. Each time the tree is submerged and coated another layer is created. 7 to 9 layers are required for this process.
5. Wax Melting with Steam Autoclave
When the ceramic layers are dry, the wax is melted with an autoclave set to 120-degrees Celsius. As the wax melts, it flows out of the mold leaving a cavity in the dimensions of the needed product. This is where the term “lost-wax” is derived.
6. Sintering
The sintering process removes any residual wax in the ceramic tree by baking it in high heat, around 1100˚C.
7. Casting
Prior to casting (pouring) the trees are heated to 1650F. The preheating of molds which is not feasible with other casting methods allows for the thinner sections to fill and corners of castings to be sharp not rounded. The next step involves melting the casting material in a 500# furnace and bringing it to casting temperatures. The sintered tree is poured with the material, set aside and allowed to cool down to ambient temperature.
8. Ceramic Mold Removal
The ceramic shell surrounding the casting is mechanically removed. To remove remaining ceramic a steel blast machine is used.
9. Finishing (Cleaning, Machining, and/or Heat Treating)
To finish the product, steel blasting is used to remove any lasts bits of ceramic material. Castings are then ground to remove any burrs. Most materials required heat treating to reach the necessary mechanical properties or for enhanced corrosion resistance. Heat treating is done in house with the furnaces designed solely for this application.
10. Inspection
The final inspection will include a measurement and material analysis report to ensure quality and specifications. If the product passes the final inspection it is sent off to their customer.
At PumpWorks Castings, we conduct complete in-house casting inspections including certified spectroanalysis, physical property testing, non-destructive testing techniques. This helps to guarantee metallurgical properties and structural integrity. All castings have traceability and Material Test Reports prior to shipments.
PumpWorks Castings Can Support Your Investment Casting Needs
PumpWorks Casting boasts a high-grade investment casting process that can handle a variety of bronze, steels, and nickels. Whether you have a medium or large upcoming production order, the experts at our industrial casting foundry in Texas are here to help.
Contact us today for a consultation or to have any production questions answered.