What Factors Affect the Castability of Metals?
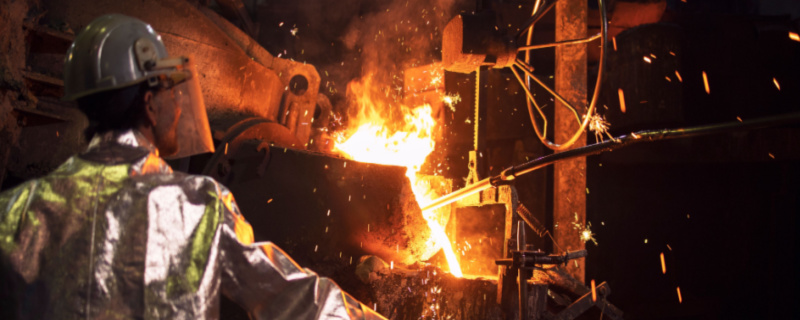
Manufacturers depend on casting, but do you know what the process is? In this quick guide, we’ll look at the definition and how different properties can affect the castability of metals.
What is Castability?
Not sure about castability and its meaning? It’s a term referring to the ease a metal can be melted and poured into a mold. It’s important to note that the metal’s properties affect its castability.
Properties That Affect Castability
Several properties can affect castability, including everything from the melting temperature to gasses escaping during casting.
Material Properties
The castability of metals depends on the properties of the materials, which include the following.
- Melting temperature. Ideally, you want to work with metals with low melting temperatures. It requires less energy, time, and expense.
- Fluidity refers to how easily the melted metal flows into the casting.
- Latent heat of fusion can have a confusing castability meaning. However, it is the amount of heat required per unit to change the metal from a solid to a liquid state.
- Specific heat is the energy used to raise the temperature necessary to melt into liquid form.
- Thermal conductivity is the cooling rate. Ideally, you want the metal to cool at the same speed to prevent the material’s cracks, breaks, and weaknesses.
- Thermal diffusivity is the rate at higher temperatures travels across the material.
- Coefficient of expansion is the castability, referring to the growth and contraction of metals in the mold.
- Resistance to hot cracking is a vital castability definition. Cooling metals are most vulnerable, and cracking is more likely to occur in metal molds than in sand ones.
- Shrinkage occurs when the metal cools, and it’s essential to account for it when creating the molds.
- Pressure tightness in metal works to prevent gasses from passing through the cooling material.
- Metallurgical purity refers to working with materials with the least impurities to prevent potential issues during the casting process.
- Chemical affinity ensures the material does not negatively react with the mold or atmosphere.
- Gas solubility is when gasses can escape from the metal during cooling, preventing the material from becoming porous.
- Vapor pressure prevents elements from escaping during heating to preserve the material’s integrity.

Raw Material Selection
The castability of metals depends on the components. It’s best to work with non-ferrous metals like magnesium, aluminum, and zinc. When selecting the materials, consider factors like melting temperature, tensile strength, and corrosion resistance. You also want to look at other properties like pouring temperature and fluidity. Not feeling these and other properties can negatively affect the product’s quality after casting.
End Product Quality
with the proper material and process, your end product should be free of defects. Potential defects can include cracks, shrinkage, or weak areas on the final product.
Geometrical Design
Geometrical designs are not always expensive to cast. The goal is to keep the process cost-effective using the proper tools. High-end equipment is typically used to prevent cracks or breaks in the finished product. The shipping process is also vital to ensure the product’s viability.
Need Casting Advice? Talk to the Experts at PumpWorks Castings
Casting can be a complicated process which is why it is also advisable to talk to the experts. The professionals at PumpWorks Castings are here to help. Whether you have questions about a metal’s castability or need additional information, contact us today to see how we can help.