6 Types of Casting Services Used in Professional Foundries
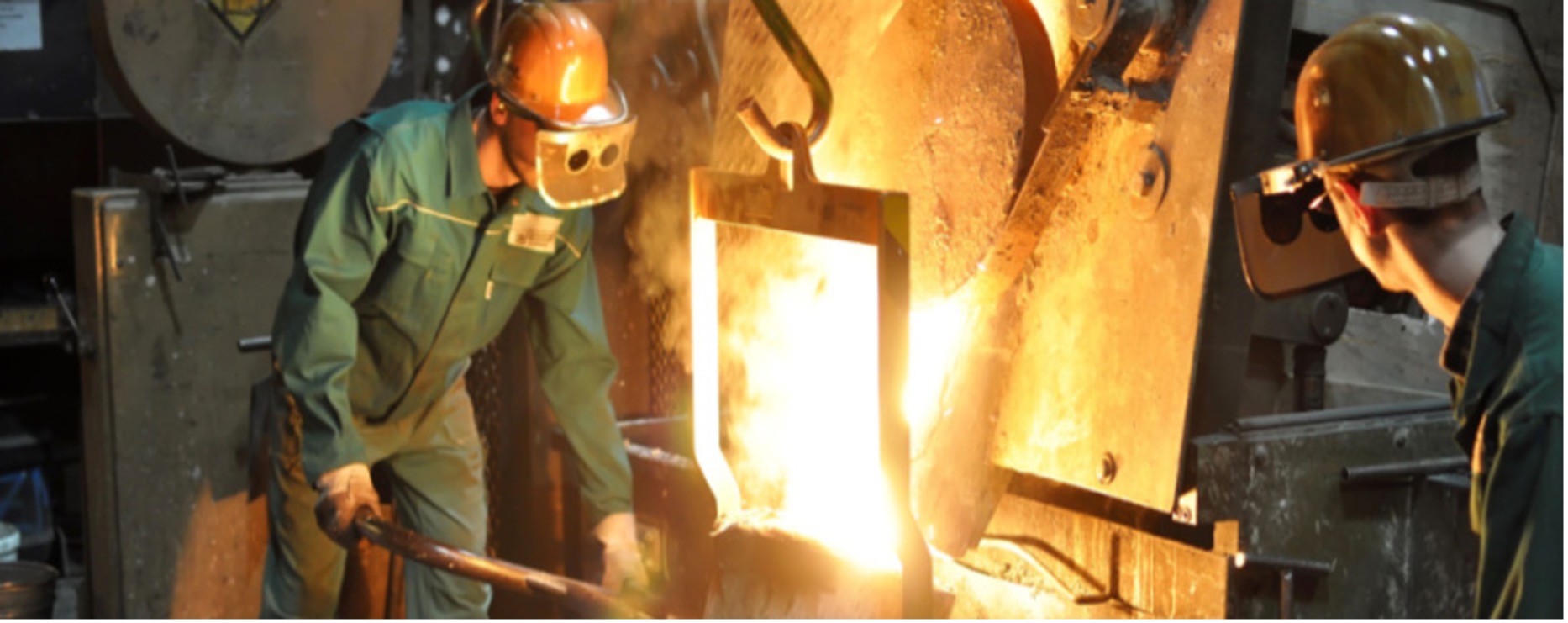
Cast materials can be found everywhere, integrated into various tools, devices, and machinery that affect how we work, play, travel, and live. Material casting is best performed under precise conditions at professional foundries to achieve the best quality components for integration in multiple applications. This article will highlight several casting services that professional foundries utilize.
Different Types of Casting
While casting is one of the oldest processes known to man, continued advances have led to improvements in techniques. With the constant integration of newer technologies, more efficient casting techniques are now available for various metal materials. Some of the most effective casting services currently employed in material casting are outlined below.
Sand Casting
This casting technique is popular in the automobile industry for creating automobile components, including engine blocks. The procedure requires molten material to be poured into a mold formed from tightly packed silica-based materials. Sand casting is a relatively cheap option for casting both ferrous and non-ferrous materials. Explore the benefits of using 3D printing in sand casting.
Investment Casting
The investment casting technique is also known as lost wax casting. Disposable wax is manipulated to form a mold into which molten material can be poured to create different configurations of finished casts. Lost wax casting produces models with high dimensional accuracy.
Learn the difference between investment casting vs. sand casting.
Permanent Mold Casting
This method combines die casting and centrifugal casting techniques to create finished components. It is done manually with molten material poured by hand into molds on a turntable. Permanent mold casting is associated with higher dimensional tolerances when compared to sand casts but is only useful for casting non-ferrous materials.
Die Casting
In die casting, molten metal is rapidly infused into a preformed mold under pressure to form the required casts. This method is very useful in casting non-ferrous materials. Foundries can regularly produce accurate models in large quantities but die casting is impractical for small-scale material manufacturing.
Plaster Casting
This casting service is very similar to sand casting, but in place of a silica mold, a mixture of gypsum, water, and strengthening agents are used to create the casting mold. In addition, anti-adhesives are typically applied to the inside of the molds to create a smoother finish on cast components.
6 Additional Casting Processes
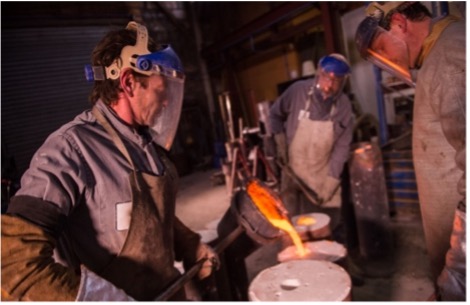
Modern foundries also integrate other processes that optimize cast production. Outlined below are some additional procedures.
1. Engineering Support
Metal casting requires specialized processes that should ideally be provided by industry experts. To create the best quality parts, engineering support from a player with extensive knowledge of metalworking, manufacturing, and casting processes is needed.
2. Pattern Making
This is one of the initial and most critical steps in cast creation as it forms the template for any finished components. Professional foundries can generate desired cast configurations from drawings or 3D models provided by their clients. Key considerations when designing patterns would include efficiency and cost-effectiveness.
3. Core Making
Every casting process requires a core designed to reproduce casts in the desired configuration. Core making processes are crucial foundry processes where the interior parts of casts are created. Cores are typically constructed using sand that is rammed, blown, or invested into a core box to produce the desired shapes. Finished cores can either be hollow or solid, depending on component requirements.
4. Heat Treatment
Some metal casting requires additional treatments to improve their tensile strengths for more specialized applications. In these cases, various heat treatment methods can improve overall strength. Heat treatments conducted in standard foundries include annealing, age hardening, quenching, solution treatments, and artificial aging.
5. Finishing
Professional foundries also provide high-quality finishing for the metal components they cast. Blasting, fettling, and hard anodizing are some of the routine finishing processes used to improve cast materials.
6. Testing and Inspection
All through the casting process, the manufactured components must undergo stringent testing and inspection to ensure they meet standardized specifications. Foundry casting will provide extensive mechanical testing and material analysis to produce high-quality casts.
Trust the Foundry Experts at PumpWorks Castings
At PumpWorks Castings, we are dedicated to fulfilling all your material casting needs. With our state-of-the-art casting foundry in Texas, you are guaranteed high-quality castings and access to the most useful advice from our foundry experts. In addition, we offer 3D-printed molds, on-site engineering services, non-destructive testing methods, professional casting design, and more.
To learn more about the professional casting services we offer, please contact us online.