What is Centrifugal Casting? Definition, Benefits & Applications
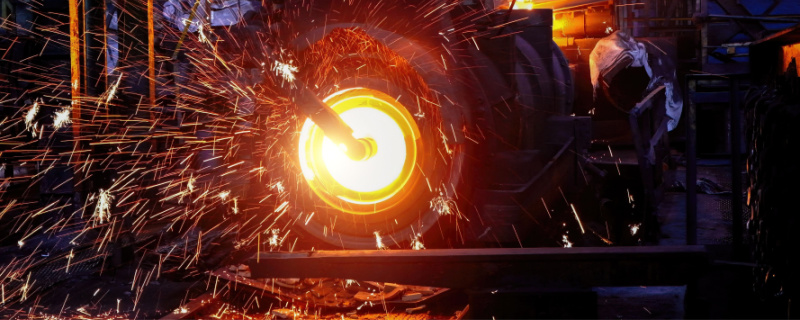
Unlike other types of castings, centrifugal casting enables the formation of hollow, solid, and intricately-shaped metal parts with minimal machining at low costs. In addition, incorporating centrifugal force into this casting process allows operators to create final products with fewer impurities and uniform, high-density exteriors. The experts at PumpWorks Castings, a fully integrated industrial casting foundry, will now explain centrifugal casting, its benefits, and its applications.
Centrifugal Casting: The Basics
Centrifugal casting (or rotocasting) includes several metal casting techniques that leverage rotation-induced centrifugal forces to distribute molten metal into mold cavities, solidifying to create a part. This casting type is essential for delivering high-integrity metal parts with considerable material soundness.
Unlike other metal casting processes, this technique exhibits high cost-effectiveness, ensuring the formation of highly complex shapes with minimal machining and low manufacturing costs. Moreover, centrifugal casting distributes the molten metal in a mold at a pressure estimated at 100 times gravitational force, resulting in superior quality metal parts. The high reliability of this process makes it ideal for hydro wear rings, jet engine compressor cases, and military item fabrications.
Process
The process comprises five key steps: mold preparation, pouring, cooling, casting removal, and finishing.
Mold preparation includes coating the cylindrical mold with refractory ceramic coating. Moreover, the step involves the ceramic coating application and mold rotation, drying, and baking. Operators achieve high-efficiency preparation by rotating the centrifugal casting mold about its axis at up to 1000 revolutions per minute (RPM).
Metal workers pour the molten metal directly into the rotating mold, allowing the centrifugal force to distribute the material towards the walls during mold filling.
Operators allow the molten metal to cool off while the mold keeps rotating. Cooling starts from the mold wall and progresses inward with time.
After cooling and solidification, operators stop the casting machine and remove the casting.
The resulting product requires proper finishing due to the impurities and bubbles that flow to the inner surface of the casting. Operators incorporate secondary processes, such as grinding, machining, or sand-blasting, into this phase of the casting process to achieve cleaner and smoother inner diameters.
Advantages
Some advantages of this casting process include:
- High cost-effectiveness
- Excellent surface finish and accuracy
- Small and thin-walled part fabrication due to cavity filling through centrifugal forces
- Denser cast parts due to their distance from the rotational axis
- Low equipment costs
- Lesser impurities in desired parts
- Manufacture of metal products with good mechanical properties
- High suitability for forming large parts
Vertical vs. Horizontal Centrifugal Casting
Vertical centrifugal casting is one where the machine assumes a vertical orientation, i.e., the die rotates about the vertical axis. This casting orientation introduces components, such as flanges and bosses, to the inner diameter of the mold. These introductions are essential for modifying the external surface of the casting from conventional circular shapes. Finished parts are sometimes non-symmetric due to the loss of balance while spinning in some cases. This type of casting is ideal for castings with a lesser height than twice its width.
Conversely, horizontal centrifugal casting assumes a horizontal orientation and is ideal for long cylindrical metallic part fabrication. The die rotates about the horizontal axis. This casting type exhibits high-speed rotation to offset gravitational forces. The mold has coverings at both ends to prevent molten metal spillages, and a pouring funnel aids the delivery of the molten metal into the mold. As a general rule of thumb, operators opt for horizontal centrifugal castings for a cylindrical part with a longer casting length than the outer diameter.
3 Types of Centrifugal Casting
Although these three processes have similar generalized steps, they differ marginally.
1. True Centrifugal Casting
This casting type is applicable for tubular metal part fabrication. The casting follows the conventional process of preparing the mold with ceramic coating, pouring the motel metal without gating mechanisms, continuously spinning the mold till the molten metal solidifies, removing the castings, and finishing the final product. True centrifugal casting allows the production of hollow cylindrical castings with high density, mechanical strength, fine-grained structure, and superior outer surface finish. Moreover, this type of centrifugal casting enables large part fabrications at high accuracy, low equipment and labor cost, and minimal scrap.
2. Semi Centrifugal Casting
This technique is ideal for fabricating solid non-hollow parts, such as pulleys, spoked wheels, brass brush, gear blanks, and nozzles. Moreover, the molds have risers at the rotation axis to feed molten metal. Operators use expendable molds around the central sprue in semi centrifugal casting to create castings with higher exterior densities compared to the center of the rotating axis. Some factors affecting the quality of the final casting include component diameter, pouring speed, cooling rate, rotating speed, pouring temperature, and mold temperature.
3. Centrifuging
Centrifuging (or centrifuge casting) is ideal for forming castings with more complex shapes by leveraging mold cavities with intricate shapes. Molten metals gain access into the mold cavity through the sprue and runner with centrifugal force. Centrifuging forms castings with varying characteristics depending on the distance from the spin axis. The casting type remains ideal for jewelry, sleeves, and small bush fabrications. Neycraft, Tulsa, and Kerr are some top centrifugal casting machines that leverage the centrifuge casting technique to fabricate jewelry and dental castings. It is noteworthy that this technique is unsuitable for alloy castings and requires the machining of the sprue and runner to get the final product.
PumpWorks Castings Can Support All Your Casting Needs
PumpWork Castings offer industry-leading solutions to your casting needs. Our several years of engineering experience and expertise is ideal for meeting all your casting requirements cost-effectively and promptly. We provide various services, including investment casting, modern 3D sand casting, and on-site engineering services.
Contact us today for more information on the services we offer.