Top Causes of Foundry Casting Defects + Tips to Avoid Them
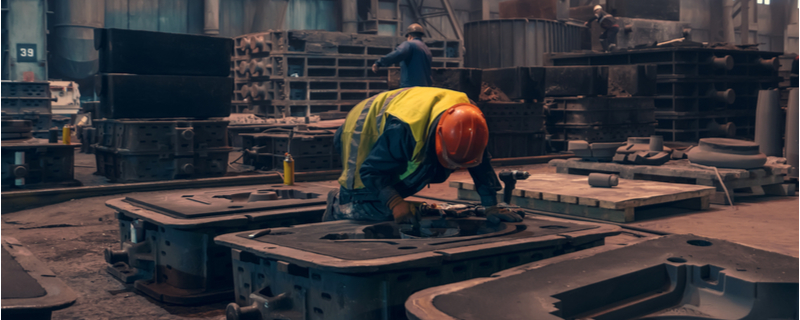
Metal forging is a delicate process that requires expert skill and knowledge. Foundries all over the world must deliver high-quality metal parts needed for various domestic and industrial applications. A key issue faced by foundry operators is casting defects. This article will discuss the most common casting defects encountered in metal part forging and how to avoid them.
6 Common Foundry Casting Defects
Metal parts forged in foundries are susceptible to various casting defects if the manufacturing conditions are not regulated carefully. Highlighted below are six common mistakes to avoid in an industrial casting foundry.
1. Shrinkage Defects
Shrinkage casting defects occur due to the difference between metal in its molten form and its solidified state. When cooled unevenly (varying temperatures at different parts of the mold), cast metal will shrink, causing angular-edged components with varying configurations that may eventually break up under stress. The various types of shrinkage defects with metal casts are outlined below.
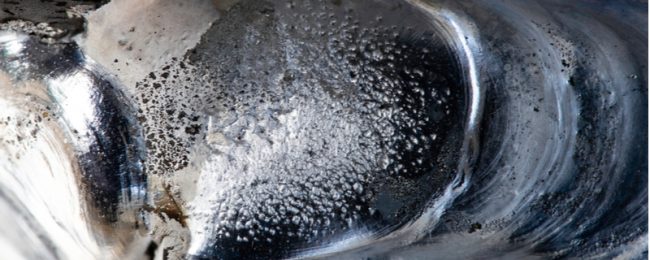
Open Shrinkage Defects
These types of shrinkage are air-compensated, occurring as dips (caved in surfaces) or holes (also referred to as pipes). The air is pulled into the mold when the metal cools, creating unwanted cast defects.
Closed Shrinkage Defects
Closed shrinkage results when unevenly heated molten material is used to craft metallic parts. The defects appear as holes in the cooled component that can be micro or macro-sized.
Warping
This abnormality of cast metal can occur both during the cooling process and immediately afterward. As a result, the cast metal part twists on itself, changing the shape and configuration from the intended template.
How to Avoid Shrinkage Defects
The prevention of metal shrinkage defects is centered around strict temperature control. Foundry temperatures must be carefully regulated to ensure even thermal conditions at all points in mold filling, cooling, and finishing.
2. Gas Porosity
Molten metal has a greater capacity to hold air than its solidified state. As a result, there is a significant risk of gas porosity defects as the metal cools and releases the gas stored within it.
Metal casting molds are usually permeable, allowing the easy escape of gases entering the process. However, permeability might drop in some cases, leading to the trapping of air bubbles and subsequent gas porosity defects. Another reason gas porosity defects occur is the presence of excessive moisture in the casting environment.
Blow Holes
Blow holes are large defects that typically occur within the cast metal but remain invisible to the naked eye. Blow holes are usually found on x-ray, ultrasonography, harmonic testing, or magnetic analysis. Blisters are thinly veiled variants of blow holes that occur closer to the cooled metal surface.
Open Holes
These are essentially blow holes that occur at a cast’s surface due to air trapping that arises as the molten metal is poured into the mold. Shallow open holes are referred to as scars.
Pin Holes
Pin holes, otherwise known as porosities, are minor defects that occur close to the surface of cast metal. They are often visible to the naked eye and are typically arranged in small groups.
How to Avoid Gas Porosity Defects
Gas porosity defects can be avoided by making the casting environment less humid. Excessive moisture must be avoided, and this can be achieved by using only dry and easily permeable sand. Additionally, foundry operators must ensure the molds and cores used in metal component casting are properly maintained and kept moisture-free at all times.
3. Mold Material Defects
These cast material defects are the most prominent component flaws encountered during metal casting. As the name implies, mold material defects are imperfections in the mold itself or the mold design.
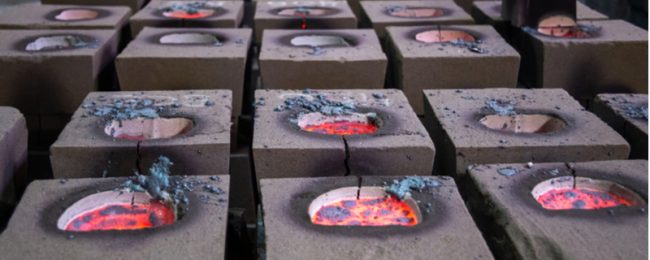
Cuts and Washes
These are caused by liquid metal erosion away from mold leaving bulges in the finished materials.
Swells
These are seen as swollen points on the finished casts due to weak molds being displaced by the molten metal.
Drops
These occur as irregular bumps on the upper parts of cast metal parts. These are also due to weak molds that cave in during casting.
Metal Penetration
Due to large, loose sand grains penetrating the casting mold creating a rough surface on finished parts.
Rat Tails
Rat tails are irregular metal defects that resemble veins. They are due to the expansion of the sand within a cast by the molten metal.
Fusion
This is a crust-like deformity on the surface of cast metal parts that possesses a shiny, glass-like appearance. This defect is due to sand melting and glossing over the cooled metal.
Runouts
Runouts are due to leaky molds, which permit the escape of some molten material resulting in a thinner cast.
How to Avoid Mold Material Defects
The most effective way to avoid mold material defects is to ensure the molds used in casting are rigid enough to withstand the stress of receiving hot liquid metal. Other helpful tips are highlighted below:
- Redesigned mold systems for cuts and washes and rat tails
- Mold reinforcement with nails and gaggers to prevent drop defects
- Early discontinuation of worn molds to prevent runouts
- The use of heat resistant mold sand to limit fusion defects
- Small even grain sizes to prevent metal penetration
4. Pouring Metal Defects
Pouring metal defects are associated with inadequate casting temperatures. Simply put, pouring metal defects occur when the molten metal introduced into a mold is not hot enough. Another reason for these flaws is a faulty gating system that allows the metal to cool before entering the mold.
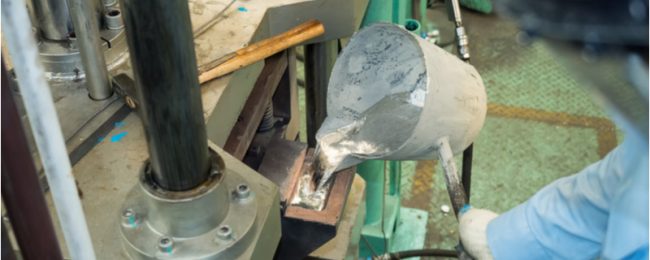
Cold Shuts
These defects occur when metal flows into a mold from two or more points but is too cold by the time it all merges. As a result, a seamless cast piece is not achieved. In addition, cracks typically occur at the midpoint of the cast, making it unstable.
Cold Shots
Cold shots are balls or splatters of excess metal that occur during pouring, cool faster than the cast piece, and become embedded when completely cooled.
Misruns
These are very similar to cold shuts. They occur when the poured metal cools before filling the casting mold.
How to Avoid Pouring Metal Defects
Preventing pouring metal defects is relatively straightforward. Maintaining poured metal temperatures at optimal levels throughout the casting process will eliminate most of the aforementioned defects.
5. Casting Shape Defects
Shape defects in finished metal casts are serious flaws that render metal components unusable. These defects are often due to improper alignment of the upper and lower portions of cast molds.
Flashes
Flashes are also known as burrs or fins and occur as extra material attached to a finished cast at the junction where the upper and lower portions of the casts meet.
Mismatches
These are typically due to horizontal misalignment of cast mold parts. When the misalignment occurs in the vertical axis, mismatches are called core shifts.
How to Avoid Casting Shape Defects
Casting shape defects are some of the most common casting defects encountered in foundry processes and some of the easiest to correct. Checking to see that all mold parts are correctly aligned and fitted in place will drastically limit the possibility of cast shape deformities occurring.
6. Metallurgical Defects
Metallurgical defects are due to inherent problems with the poured metal. Impurities in the poured metal cause slag inclusions. Hot tears are typically due to poorly designed molds that allow cast shrinkage. Hot spots are due to imbalances in metal composition and poor mold design, and uneven cast cooling.
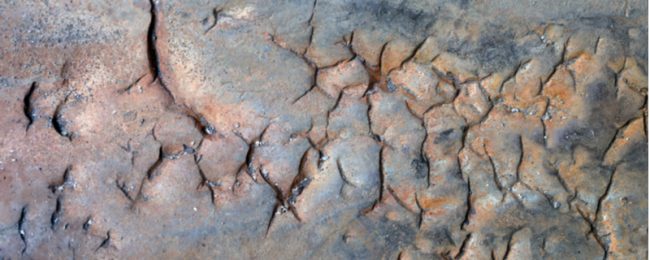
Slag Inclusion
Slab inclusions are uneven crusts that form in poured metal when molten material with slag particles is introduced into a mold.
Hot Tears
These cast deformities are due to the contraction of cooling metal. While still solidifying, the poured metal is weak and cooling results in irregular cracks and fissures.
Hot Spots
These defects are due to uneven cooling, where some spots in a poured cast cool off faster than the rest of the pour. This results in areas of unusual hardness that can wear out tools and make machining more cumbersome.
How to Avoid Metallurgical Defects
Proper mold preparation is key to preventing hot spots and hot tears. Well-designed molds and adequate composition of molten material are highly effective in preventing hot spots and hot tears. Additionally, using molten material devoid of slag particles will prevent irregular metal crusting.
Contact PumpWorks Castings for Quality Casting Products
PumpWorks Castings is a first-class industrial casting foundry located in Lufkin, TX. With an accommodating and experienced quality assurance team, you can rest assured that your metal casting needs will be fully catered to.
Contact our team today to get started.