A Beginner’s Guide to Casting Design
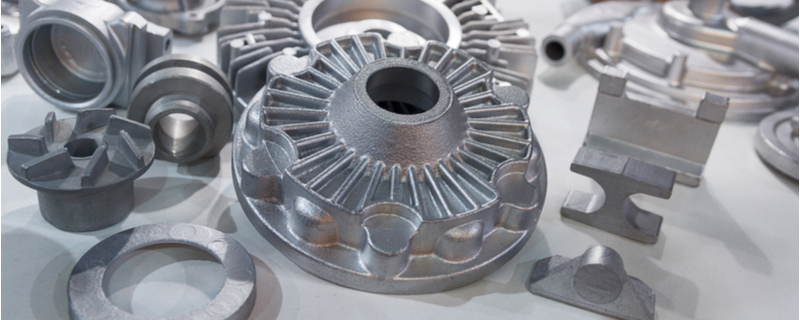
An ideal casting design will make a huge difference in creating a mold—no matter how simple or complex. Often, the casting process calls for expertise in the right type of metals and casting techniques to ensure the best quality of casting is produced. Keep reading to learn all about the casting design process.
What is the Casting Design Process?
The casting design process is a manufacturing process where molten material like a liquified metal is poured into the casting mold of a specific shape and allowed to cool or solidify within the printed mold. Once the metal solidifies, the casting is removed by breaking the mold or ejecting it.
Different Types of Casting Processes
There are varying types of casting processes, including:
- Sand casting process
In this type of casting, liquid molten metal is poured into the casting mold of the desired shape and allowed to solidify. The solid metal is then removed by breaking the mold. Discover the benefits of using 3D printing in the sand casting process.
- Die casting process
This casting process involves forcing molten metal into a casting mold under gravity or high pressure. For that reason, the die casting process can take the form of gravity casting or pressure die casting.
- Investment casting process
Here, wax is the pattern material, and cement concrete is the mold material. Also, check out our investment casting services at PumpWorks Castings.
- Shell mold casting process
Shell mold casting, also called shell molding, is where the mold used is a thin hardened shell of sand.
Factors to Consider When Designing a Cast Component
You need to bear in mind many casting design considerations every time you cast a specific product. Here’s an overview of the most important nuances to be aware of.
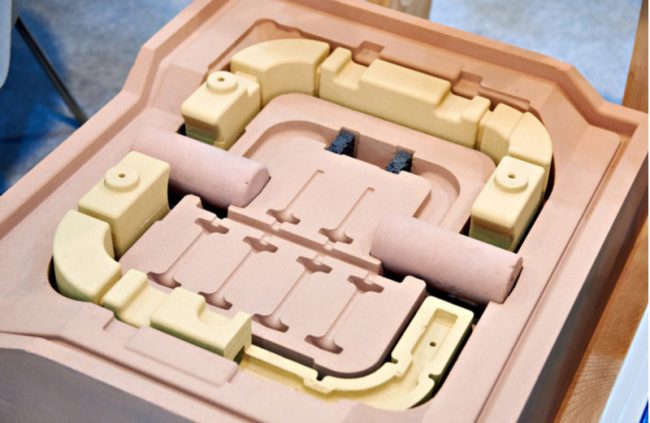
Appearance
The product’s look is perhaps the most important consideration during the design process. Ideally, this is the first thing that customers look at. Therefore, the appearance of the product is something you shouldn’t overlook.
Assembly Method
After product aesthetics, the next important thing to consider is assembly. But, again, this is another crucial thing that a customer interacts with.
Function
If the product isn’t functional, customers are likely to forget all about how beautiful the product looks. Therefore, when designing a cast component, keep the functionality in mind to ensure that it meets its intended use.
Material
Another integral aspect to mull over is the product’s material. Customers will want to evaluate the end product based on its expected life. Thus, the sand casting core design should also prioritize settling for the best material.
Apart from these factors, incorporating the following tips during the casting process will increase the likelihood of succeeding in your mission.
4 Helpful Casting Design Tips for Success
1. Design for Manufacturing
Design for manufacturing (DFM) is a vital aspect of the product development cycle. This entails optimizing your product’s design for the manufacturing and assembly process, combining the product’s design requirements with the production method. Ideally, using DFM lowers the cost of producing a product, and it helps to maintain its quality.
2. Pay Attention to Wall Thickness
Based on the casting design guidelines, wall thickness is a vital parameter you should pay close attention to. Thin wall sections often lead to breakage of parts, especially during the manufacturing process. At the same time, thick wall sections can also lead to casting defects and an increase in weight.
3. Incorporate Drafts
You should also be wary of the draft angle. Incorporating drafts is crucial if you want to produce a cast component with uniform quality in large volumes. This is very important, especially if you will be working with die casting mold design.
4. Choose a Parting Line
More importantly, choose your parting line wisely because this will simplify the casting process and lead to a high quality of products.
Contact PumpWorks Castings for All Your Casting Design Needs
Relying on expert knowledge when it comes to casting design can make a huge difference in getting the best product design of your choice. At PumpWorks Castings, we offer nothing but the best casting solutions in the USA. You can always turn to our fully-integrated industrial casting foundry when quality casting design is what you need.
Contact us today to get started.