Casting vs. Forging – Which One Is Right for You?
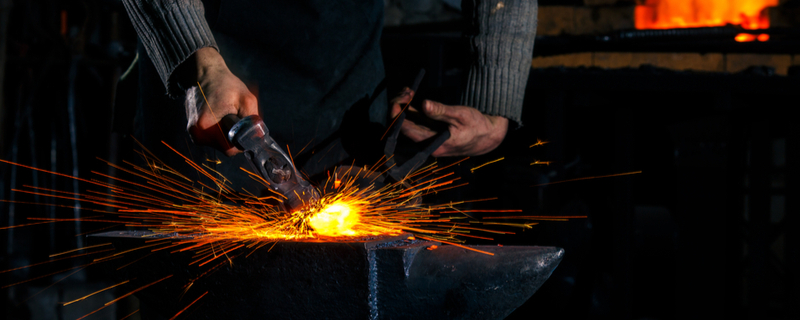
The components used in various industrial and commercial equipment are created using multiple methods. The most commonly employed techniques include casting and forging. The method employed is dependent on various factors, including raw material availability and end-user specifications, amongst others. In this article, we will determine the best method for you and the right materials to achieve optimal results.
What Is the Difference Between Forging vs. Casting?
The key difference between casting and forging is how the finished metal components are formed.
Casts are formed when heated molten material is poured into a cast mold and left to solidify into desired shapes. Casts typically require very high temperatures to achieve the required material shapes.
On the other hand, forged materials may or may not involve the use of extremely elevated temperatures to craft material into the required shapes. Forging is done using compressive forces and may be done cold (forging conducted at room temperature) or warm (the target metal is heated above room temperature but below the recrystallization temperature.)
Further, there are differences in the tensile strength of metal components produced by casting and forging. Forged materials are typically stronger and less likely to shatter under stress compared to similar cast materials.
Forge: Defined
To forge a metal component, the target material has to be subjected to repeated die or hammer strikes which gradually craft it into the desired shape. Repeated deforming and shaping can be done either under elevated thermal conditions or at room temperature.
Pros:
- Creates tougher metal components
- Less brittle
- Does not typically require extreme temperatures
- Produces materials with finer grain size and continuous grain flow
- Porosities, cavities, shrinkages, and other defects associated with metal casting are eliminated
- Improved wear resistance
Cons:
- Increasing difficulty in forging larger, bulkier materials
- Costlier process than metal casting
Best Materials for Forging
The metals chosen for forging are largely dependent on the ease of accessibility and production capacities of the manufacturer. Potentially every metal can be forged, but the most commonly forged ones are listed below:
- Alloy steel
- Micro alloy steel
- Carbon steel
- Stainless steel
- Titanium
Cast: Defined
Metal casting is a process that requires molten material to be delivered into a pre-determined mold and allowed to cool into its final shape. Casting can be used to create intricate finished components but always requires markedly elevated temperatures to turn the metal into its liquid form.
Pros:
- Complex shapes and designs are created easily
- A broader range of alloy selection
- Smaller production cycles are cost-effective
- Produces lighter parts than forging
- Casting involves cheaper tooling
- Cheaper processes
- Shorter manufacturing times
- Few size limitations, bulky parts can be cast with ease
- Multiple casting techniques available to suit individual manufacturer needs
Cons:
- Casting defects are common
- Higher risk of metal wastage
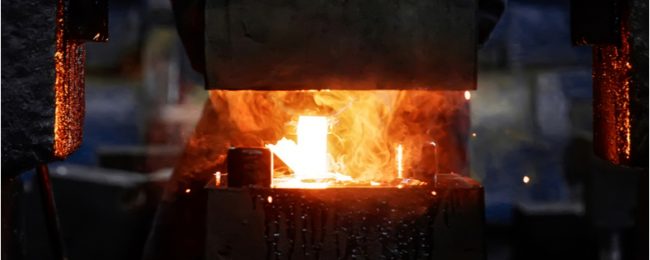
Best Material for Casting
There are several metals suitable for casting with methods that date back to early times.
Some common metal raw materials still in use in modern casting methods include:
- Zinc
- Steel
- Copper
- Aluminum
- Gray iron
- Ductile iron
Cast or Forged: How can You Tell?
An interesting dilemma sometimes encountered with industrial parts is determining whether they were cast or forged. Casting materials and forging materials are often similar, so an accurate differentiation can’t be made solely based on the raw metal utilized.
The easiest way to differentiate products created from the two processes is by simply confirming the steps in the manufacturing cycle they underwent.
Forging vs. Casting Cost
There are various factors contributing to the cost of producing cast metal parts or forged metal components. The major determinants of price include:
- The volume of materials being crafted at a time
- The nature of the alloy to be forged/cast
- Specifics of the casting or forging processes
- The complexity of the final design
For moderate to large lot sizes, forging can be used to generate the desired materials. On the other hand, material casting is a more versatile method that can be used to create finished materials in small, medium, and large lot sizes.
Furthermore, the materials and equipment required for metal casting are typically cheaper than those needed in metal forging. Overall, both methods can be used to create satisfactory finished products, but the choice of method should warrant careful consideration of the factors outlined above.
Ask the Experts at PumpWorks Castings Which Process is Best for You
At PumpWorks Castings, we focus on crafting and delivering the highest quality metal parts. With a state-of-the-art industrial casting foundry located in Lufkin, we are uniquely positioned to cater to all your metal casting needs.
To get in touch with our expert team, please contact us today!